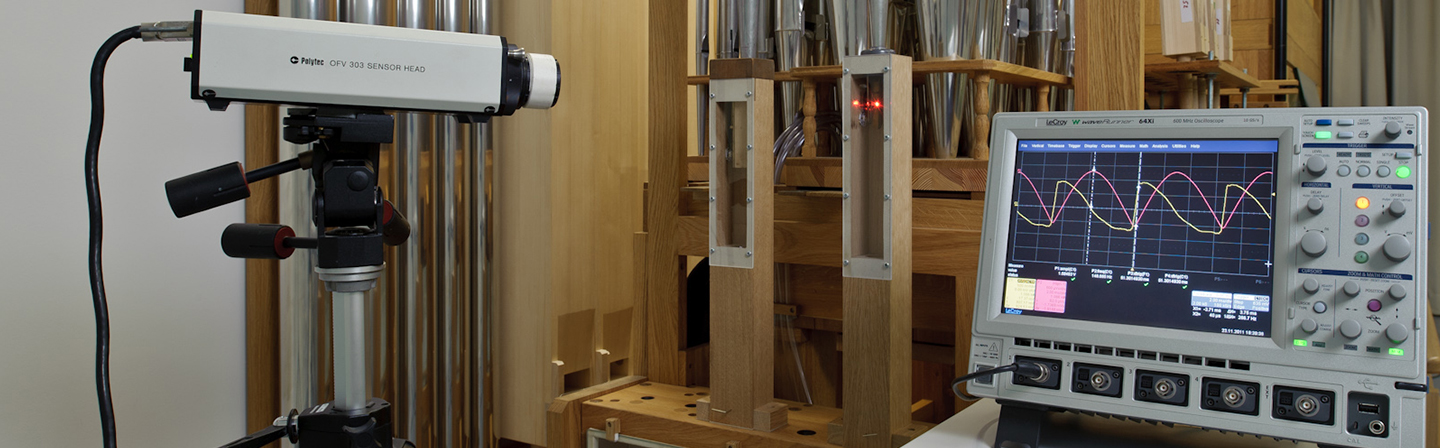
Acoustics
Laser scanning vibrometry enables non-contact vibration analysis for a wide variety of objects. Using a customizable measurement grid and automatic scanning, the system captures detailed vibration data, making vibration patterns visible and rendering them as videos. With a frequency range of up to 40 kHz and a broad measurement spectrum, the technique meets even the most complex requirements. It is suitable for analyzing machines, devices, tools, and components, accomodating both structure-borne and airborne sound excitations. With the ability to export data for modal analysis or simulation into external programs makes laser scanning vibrometry a flexible and powerful solution for optimizing vibration behavior and noise emissions.
Our laser scanning vibrometry services provide not only precise measurement data but also customized solutions for your specific requirements. Our analyses help you identify vibration issues early, acoustically optimize your products, thus securing a competitive edge. Rely on the experience and innovative strength of Fraunhofer IBP to deliver products that excel quality and performance.
How can we assist you? Learn more about our range of services or send us an e-mail.
Measurements | Vibration velocity and displacement, vibration and modal analysis |
Measurement object | Machinery, equipment, installations, tools, components, panels, shells, etc. |
Technical data
Laser | Helium-neon laser (λ = 633 nm) |
Frequency range | 0 to 40 kHz |
Measuring range | 0.5 μm/s to 2.5 m/s (vibration velocity) |