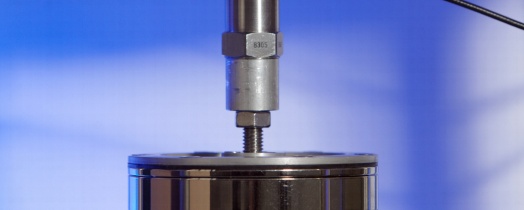
Acoustrics
A few years ago, a test rig was developed at the Fraunhofer Institute for Building Physics IBP in Stuttgart for measuring the dynamic E modulus and loss factor based on ISO 6721-4 (non-resonant method). This method can be used to examine the E modulus and loss factor of foams and soft plastics (such as rubber, silicone, etc.) as a function of frequency.
However, it is not possible to calculate a general limit for the usable frequency range, as this depends on the material in question and the thickness of the sample, in conjunction with the thickness resonance of the respective material. With the materials examined so far (various silicones and different foams), in some cases sufficiently accurate and fully reproducible results could be obtained for the modulus of elasticity and loss factor up to 2,000 Hz. This is, however, highly dependent on the material.
Benefit from our researchers’ expertise to reliably determine the dynamic properties of your elastomers. Our measurements provide you with detailed information about the performance of your materials, thus helping you to fully exploit their application potential.
We are also happy to assist you in measuring the dynamic modulus of elasticity and loss factor. Our experts look forward to hearing from you.
Measurement | Elastic (Young’s) modulus, mechanical loss factor |
Standard | Based on ISO 6721-4 |
Measurement object | All types of elastomers (plastic and foamed materials), sealing compounds (silicone, acrylic, etc.), elastic adhesives |
Technical data
Size of material samples | Diameter 20 mm (cylindrical slices) |
Thickness of material samples | 3 to 5 mm |
Shape function | The influence of geometry is considered by using a shape function. |
Frequency range | 50 to approx. 3000 Hz (upper limit depends on the sample) |
Special feature
Sample preparation | Preparation and hardening of the sample is carried out outside of the test system. Afterwards the sample is installed with adapters on both sides. |